Jason M. Barr February 10, 2020
Note this is the first post in an intended series on the technological and economic barriers that need to be broken to construct the first mile-high skyscraper.
The Illinois
In 1956, Frank Lloyd Wright unveiled his design for a mile-high skyscraper (1.61 km)—The Illinois. It was to be built in Chicago and was to have 528 floors, with 12.3 million square feet (1.14 km2) of office space for 123,000 people. Commuters could choose from 15,000 parking spots after they arrived by one of four feeder highways. Two helicopter landing decks could accommodate 50 helicopters each.
Ironically, Wright was, at best, ambivalent about skyscrapers. In 1923, after witnessing a devastating earthquake in Japan, he expressed his belief that “the skyscraper, never more than a commercial expedient…is become a threat, a menace to the welfare of human beings.” He spent much of his career promoting his “Prairie Houses” and planned, decentralized communities, such as his Broadacre City.
And yet, at age 89, he felt compelled to produce his mile-high design. The building was, of course, merely a concept—an imaginary figment of architecture and engineering. It was never meant to be built, as the ability to construct and operate it was nearly impossible. But ideas are powerful motivators, and when a man of Wright’s stature proposes such a thing, it becomes part of the vast ocean of our collective consciousness. And just as importantly, it was produced by America’s greatest 20th-century architect when America reigned supreme in the world of skyscrapers.
Regardless of his motivations, his renderings have launched an architectural and engineering quest. The mile-high has become the Holy Grail of skyscrapers. To build one is the burning ambition of many throughout the world, particularly in Asia. Whoever constructs it will beat the odds and grab ownership over something that was once purely an American phenomenon. After all, one mile—5280 feet—is as an arbitrary length as anything else, except that it’s the standard of measurement in the United States.
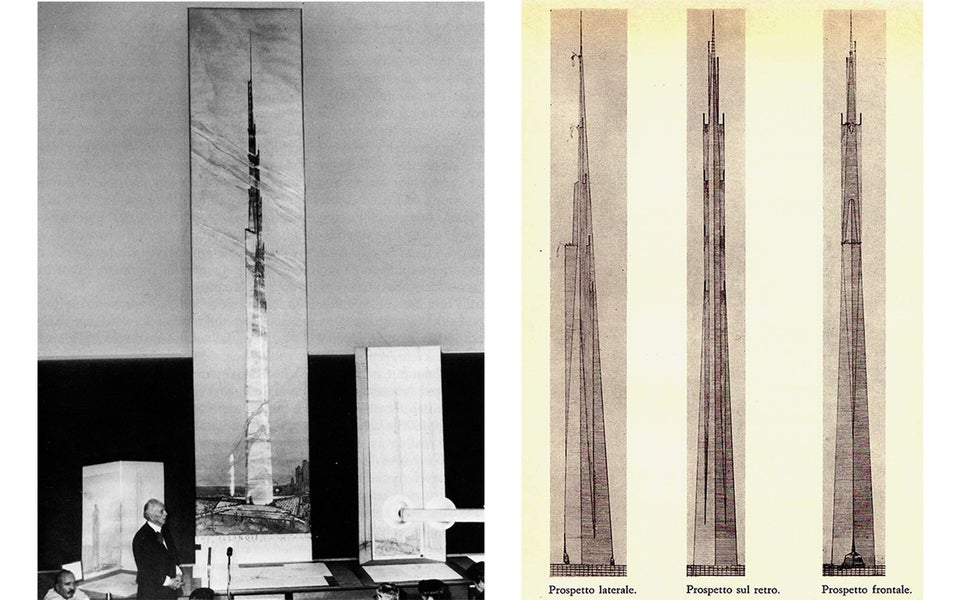
A Brief History of Bottlenecks
If we step back and take a broader view of skyscrapers, we can think of each one as part of an economic and technological system of interconnected parts. The key demand-side components are the prices that occupants are willing to pay, the uses of the structure (residential, commercial, etc.), and any additional or secondary benefits, such as advertising, placemaking, or the quest for glory. The supply side comprises the cost and logistics of construction, the technological and engineering aspects, the architectural style, local building regulations and interactions with local officials, and access to financing and capital. At any one time, the different elements are acting more or less strongly to move construction in a particular direction.
Across the World
Across the world, urbanization and economic growth are pushing developers to go taller. Technological innovation is also lowering construction costs. This rising demand and falling costs are naturally producing a rise in the “economic height” of tall buildings, where the economic height is the height that maximizes the profits from construction. But, arguably, global competition is driving cities and developers to increase building height beyond this economic height for the secondary gains they may produce. We can call this extra height, “symbolic height,” since it’s meant to convey additional information about either the city, the developer, or the occupants.
The point here is that the demand for the world’s tallest buildings is based on some combination of economic and symbolic heights. Economic height must get a builder to a certain level. Then the symbolic height can do the rest since the building must generate enough profits on its own so that the cost of the additional height can be paid for, or, at least, doesn’t bankrupt the developer. There is a constant drive to increase the height of the tallest buildings in an attempt to stand out. The ability to stand out, however, depends on the height of surrounding structures. If the economic height is increasing through rising incomes and falling costs, then symbolic height must be increasing as well.
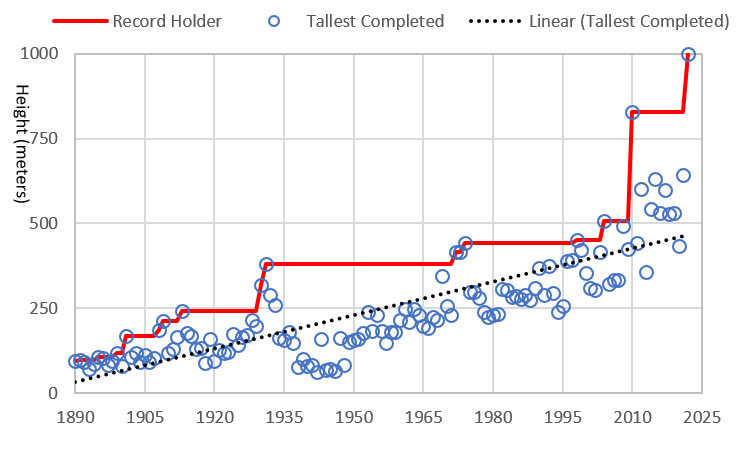
A Theory of Technological Evolution
Developers are continually seeking ways to push the technological envelope. While there is no one universal way that technological change occurs, I’d like to offer what I call a Theory of Bottlenecks. First, a boost in demand produces a supply bottleneck, in the sense that the need for tall buildings outstrips the current technological ability to satisfy it.
This bottleneck drives a “revolution”—a package of new technologies that allow for the solution to this problem, so much so that they provide opportunities for new record-breaking heights. Then, over time, engineers and developers tinker with the technologies, making incremental improvements that help lower the costs of construction within the “reigning” construction “paradigm.” At some point, demand catches up with supply, which produces a new set of bottlenecks that need to be removed with new technologies, and the cycle begins anew.
The Bottleneck Cycles
I would like to argue that since around 1880, there have been three bottleneck cycles. The first one began in New York and Chicago in the 1880s and culminated with the Empire State Building in 1931, at the end of the Roaring Twenties. During this time, the steel frame and electric elevator “package” were continually perfected. The Great Depression and World War II, however, wiped away demand. After that, there was a period of rebuilding. Economic growth and the evolving nature of work eventually produced a need to go even taller.
The Structural Revolution of the 1960s
The issue with the standard steel-framed building is that as it goes higher, it requires an increasing amount of steel per floor to brace the structure against the rising wind forces. This so-called premium for height, generated the second “skyscraper revolution,” as initiated by engineers such as Fazlur Khan at Skidmore, Owings & Merrill (SOM) in the 1960s. Advances in computing for engineering design combined with creative “thinking outside the (steel) box” lead to new structural forms.
These innovations helped to make the construction of supertall buildings cheaper while increasing the total rentable area of each floor. Khan, for example, was a pioneer in the tubular design. In older buildings, such as the Empire State Building, a latticework of columns and beams form the structure. The tube design, however, uses many thin steel columns placed closely together around the facade. Each column is connected by a horizontal “spandrel” beam. It allows the façade to do most of the heavy lifting, so to speak.
The John Hancock Tower (875 North Michigan Avenue) in Chicago, completed in 1968, represents one of the first of the post-War supertalls to use this tubular design (along with diagonal “x-bracing” to help improve rigidity). The building, designed by SOM, with Fazlur Kahn as the chief structural engineer, promoted a “jump” in heights beyond those at the time. Versions of the tubular design were then used for the record-breaking Twin Towers in New York City and the Willis (Sears) Tower, which were all completed in the early 1970s.
The 21st Century
A 21st-century “revolution” has, in large part, been driven by the tremendous demand for skyscrapers in Asia. In the last quarter-century, the world has seen a whole new suite of building technologies that are allowing for even greater heights. Examples of these include the buttressed core; high-strength, pumpable concrete; the mass-tuned damper; and wind tunnel testing. These innovations are being employed in the Burj Khalifa and the Jedda Tower. They have allowed height to leapfrog, once again, beyond the economic demand.
The Elevator Problem
Although structural systems have undergone dramatic changes, the elevator is still based on the traditional rope-based method, where a cable is attached to the elevator car to move it up or down. However, as buildings go taller, the ropes must get longer as well. And rope weight increases exponentially with height, which increases not only the cost of operating the lifts but the risk of the cable snapping. As Professor Kheir Al-Kodmany writes, “In very tall buildings, almost 70% of the elevator’s weight is attributed to the cable itself, and when the rope gets too long it cannot support its own weight.”
Elevator suppliers have been hard at work, developing alternatives to the steel rope. One of the most promising is the “UltraRope” developed by KONE. It is comprised of a carbon-fiber core with a special high-friction coating, making it extremely light and hearty. The UltraRope is helping to break the one-kilometer bottleneck. It is going to be installed in the Jeddah Tower in Saudi Arabia, which, when completed (likely in 2022), will the world’s tallest building at one kilometer high (3281 feet).
The Ropeless Future
However, according to Prof. Michael Cesarz, CEO of MULTI at ThyssenKrupp, the rope remains one of the key barriers to increasing maximum building height. At some point, new heights will not be feasible with a rope-based elevator, either because of limits on cable strength or because of rope vibration. As Professor Al-Kodmany writes, “[L]ong cables cause damage to the shaft and to themselves. For example, in the former World Trade Center Twin Towers, the elevators’ cables swung back and forth in the building, and over the decades, their movements resulted in wearing deep holes in the shaft walls.” The problem is even more severe in seismic zones, where an earthquake could cause buildings to sway. While structural technology prevents the skyscraper from collapsing, the rope is still vulnerable.
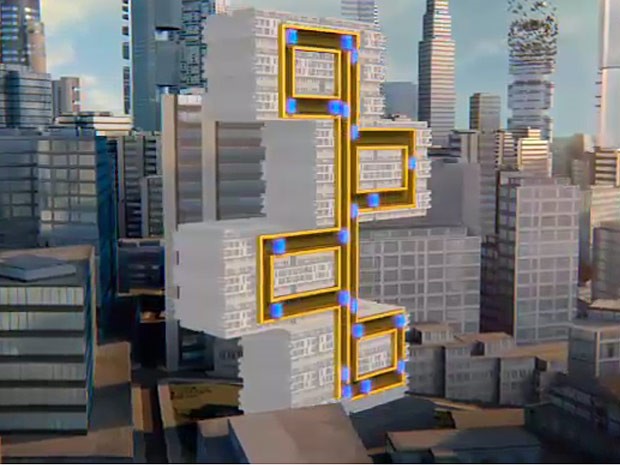
The Maglev MUTLI
Frank Lloyd Wright, with a wave of his hand, dispensed with ropes in The Illinois. Instead, his fictional building used fictional nuclear-powered elevators. But today, one elevator company, ThyssenKrupp, is betting on a ropeless future. It is developing the MULTI, an elevator that travels by magnetic levitation (maglev).
The technology is now used for bullet trains. For example, Shanghai has one to ferry travelers from the Pudong business district to the airport. It can travel up to 268 miles per hour (431 km/h). The maglev system has the cars hovering over tracks, so there is no friction. The principle is the same for elevators, but they are, of course, used to run up and down.
Without a rope, multiple elevator cars can run in the same shaft, and their movement can be coordinated with sophisticated software algorithms. When one is needed on a higher floor, other cars, which might be in the way, can move horizontally to free the path. According to Prof. Cesarz, the ability to move cars aside represents one of the last remaining bottlenecks for the maglev elevator itself. ThyssenKrupp engineers are close to perfecting the switching device that will make the MULTI practical. The company has even constructed an 807-foot (246-meter) testing tower in the German town of Rottweil. When the elevator cars can seamlessly change directions, they will circulate through the building like blood cells in our arteries.
Maglev elevators are likely to have many benefits. In the immediate future, by allowing several cars to run in the same shaft, they reduce the total amount of shaft space, meaning more revenue-generating space for the building owner. Further, it can more efficiently carry people to their final destinations within the building. Since ropes are heavy, they require significant energy usage. The MULTI can reduce both energy costs and greenhouse gas emissions.
Other Possibilities
But once the rope is eliminated, architects, engineers, developers, and planners could, in theory, exploit endless possibilities—to make the MULTI the iPhone of real estate. The ability to run many cars through the shafts could mean a more personalized elevator experience. We can imagine a situation where each tenant has their own elevator. Say an apartment dweller arrives home; she calls her car, which retrieves her on the ground floor. Upon arrival, say on the 40th floor, the unit “plugs itself in” to the entranceway, and waits for the next trip down. But more interestingly is the opportunity to connect buildings via skybridges. Without the ropes, there is no need for an elevator to remain inside the structure. Thus freed, it could offer a fast way to travel from one building to another.
Releasing the Bottleneck
When the MULTI is operational, it will likely get us that much closer to Wright’s vision of the mile-high skyscraper. But the question remains, is the elevator the only bottleneck preventing the mile-high from being built? For the answer to that, you’ll need to stay tuned.
Continue reading related posts. The “Technology of Tall” series is here. The “Economics of Skyscraper Height” series is here.
[…] Skyscrapers were built to accommodate the city’s rapid growth. Land values were rising while engineering and construction technology were improving—these two factors, more than anything, explain the height […]