Jason M. Barr (@JasonBarrRU) June 4, 2019
Note this is Part IV of a series on the economics of skyscrapers. The rest of the series can be read here.
Rise of the Skylines
As we look around planet Earth, we can’t help but notice that skyscrapers are getting taller. In 2000, for example, the average height of the tallest 100 completed buildings was around 285 meters (935 feet). In 2018, that number was about 385 meters (1263 feet), for an average annual growth rate of 1.8%. What is causing this rise in building height?
The Demand for Height
First and foremost, skyscraper construction is demand driven. Tall buildings are built to satisfy our need and desire to be together in dense urban areas. The more humans base their economies on services and intangible products, they more they are drawn to cities. The masters of finance, marketing, business services, and high-tech need to cluster together in order to make their products. Also, the great wealth generated by this productivity fuels the growth of the consumer-oriented city, and its concomitant suite of cultural and entertainment-based amenities. The quest for a better life draws people to the same place at the same time. The skyscraper is thus a solution to the problem—it is a machine that converts air to land.
The Supply of Height
But here I want to argue that to really understand skyscraper heights, we need to investigate not only the demand for tall buildings, but also the forces that create their supply. If we want to understand building patterns around the world in places like China or the United Arab Emirates, we need to study the costs of construction in these places. The rise of skylines in Asia is as much as due to the cost side as it is to urbanization and the increasing importance of global cities.
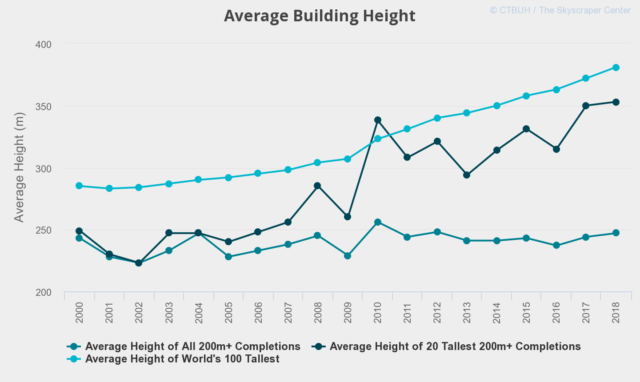
The Economic Theory of Skyscraper Height
But, before we dive more deeply into the costs of building a shiny new skyscraper, we first pause to discuss the economic theory of skyscraper height. The economic height of a structure is the one that makes the most sense in terms of best balancing the demand for height with the costs of providing it. If we did some economic modeling, what pops out is an equation for the optimal building height (based on some simplifying assumptions). Though one can find a more detailed treatment here, the bottom line is that this equation can be given in a simplified form:
Economic Height = (Market Price Per Floor)/(Construction Costs Index Value)
Or for simplicity:
H=P/C.
That is, the economic height is given by the market price per floor, P, relative to a measure of construction costs, C, which includes the prices of materials and labor, and the efficiency of the construction operation.[1] We can observe from the equation that, all else equal, the lower the value of C, the taller a building will be in a given city at a given time.
P
If you want to understand the near-universal pattern of why there are tall buildings in the city center and low-rise building further away, then just look at the nature of the market prices per floor (or per square foot or meter), and you will see they drop off rather steeply as one moves further away from the center. That is to say, within a city, at a given time, we can assume that C is about the same for all builders. It’s P then that measures what building occupants are willing to pay at various locations.
And P can be broken down into, roughly speaking, two parts. Part I is the quality of what’s inside the building (does it have fast elevators, great views, marble floors, etc.?). Part II is the quality of what’s outside the building—its location. This is the key reason why buildings are so tall at the center—the location (or land) value is so high. Wall Street firms need to cluster together to earn greater profits and they pay for the right to do it. Developers respond to the high willingness to pay by going taller. The desire to pay falls rapidly as one moves away from the center. This has been strongly documented around the world and over time.

A Moving Target
Skyscraper height is thus determined by the ratio of the benefits to the costs. If we want to understand height at a given time in a given city, then using the prices at various locations is a decent indicator of about how tall a building should be. But if we want to compare this economic height over time and/or across cities then things get more complicated—both P and C become moving targets.
Compare New York to Shanghai, for example. The average height of the two cities’ completed skyscrapers since 1988 have been similar. But the question we cannot decipher is what are the relative prices to costs? In New York, both prices and costs are higher than in Shanghai; and yet the ratio is about the same. Asking rents in the new 67-story One Vanderbilt tower adjacent to Grand Central Station are up to $160 per square foot ($1,722 per square meter). The 128-story Shanghai Tower, evidently, has asking rents of half that amount (and now you get a sense of the relative costs of building in these two cities that generates the same average heights).
Roaring Twenties
This equation can also help us understand the building boom in New York during the Roaring Twenties. P was rising because of the growing economy, and C was falling due to technological innovations and learning-by-doing. When you put the two things together you can a rapid rise in the heights of buildings.
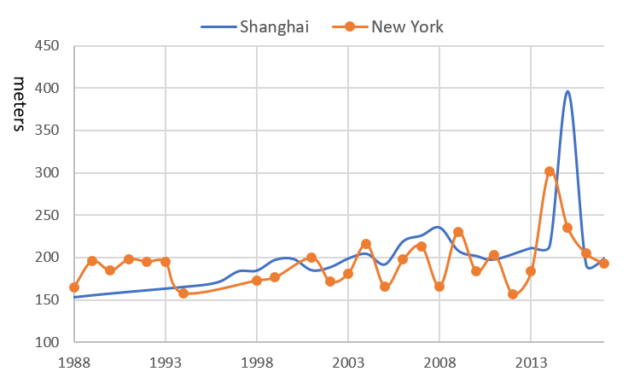
Global Costs
One of the key drivers of costs around the world are wages. An unskilled construction worker in New York, for example, is paid $17.57 per hour. In India, laborers get paid $0.63 dollars per hour. While the same type of workers in China receive about $3.36 dollar per hour. Since labor costs represent a substantial fraction of total costs (in the U.S. they can be as high as half the costs), the less developers must pay for labor, the lower the costs, and thus the more likely they are to build taller.
Consider some examples (in non-inflation adjusted U.S. dollars). One World Trade Center cost nearly $4 billion, as compared to the Shanghai Tower, which cost $2.4 building to construct. On a per-floor basis, that’s nearly double the costs. The Burj Khalifa, is almost 300 meters taller than One World Trade Center, yet the total costs were 61% less! The idea of getting a 163-story building in New York for $1.5 billion is laughable.
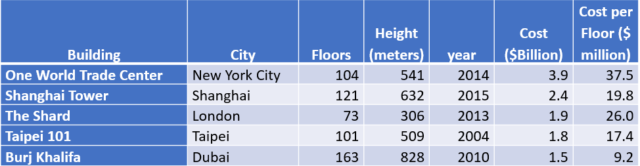
A Skyscraper Cost Index
To investigate this issue in more detail, I created an index of skyscraper construction costs around the world. The website, Emporis.com, lists the costs of 200 large high-rise buildings. (Details about how I created the index can be found here). It is, admittedly, a first attempt to measure skyscraper construction costs. A more detailed analysis is made difficult by the fact that developers (or their general contractors) generally do not release the cost of construction and so I need to use the limited publicly available data.
But what the exercise shows is that, relative to the U.S., mainland China and the Arabian countries can get skyscrapers for a substantial discount relative to the United States (and even more so compared to New York City).
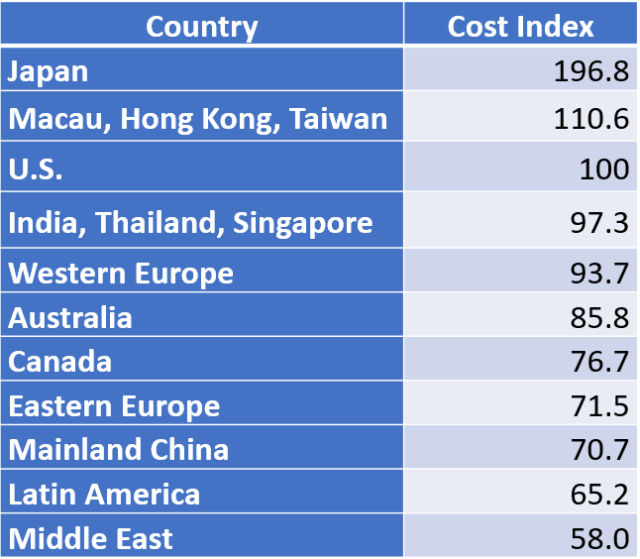
Costnomics
But an index value doesn’t tell how total costs change with building heights, it only gives a measure of the average costs of construction. To better understand the economics of building height, we need to dive a little deeper. Let’s take the point of view of a developer. Say we own a large lot in an office district in downtown Barropolis. We know (approximately) the average rents we can expect to earn once the building is filled, since we can observe the rents being paid in similar towers. This means that in order to maximize the profit, we need to determine how our total costs change as we go higher, in order to find the sweet spot.
It’s generally believed that average costs per square foot or meter are u-shaped with respect to floor height. For smaller buildings, going taller means that the per floor costs are falling, and then, at some height, they begin to rise. At that point, the costs of providing an additional floor becomes greater. For example, the cost of adding the 51st floor is more than the cost of adding the 41st floor. Where that turning point is remains an open question, and, as I will show below, it seems to be different in different cities.
The economic theory of skyscrapers says that the profit maximizing developer keeps adding floors until the revenue of the last floor just equals the cost of providing it. One floor less means leaving money on the table since the revenue from another floor will be greater than the cost. Building one floor above the profit maximizing height means losing money since the cost of the last floor was greater than the revenue is generates.
More Concrete
So why do the costs of adding more and more floors rise after some point? The answer has to do with the nature of building tall. Going taller and taller requires thicker materials, such as concrete or steel, on the lower floors to support the superstructure (as do the internal elements such as plumbing and electricity). Similarly, the cost of the foundation rises as the building gets taller because the it needs to support more weight.
Swaying in the Wind
Next is the additional costs of wind bracing. Tall buildings are constantly being bombarded by the wind. The taller the building, the greater the wind pressure, and the greater the possible sway. Nobody wants to be inside a building that feels like being on a 19th century whaling boat. Thus, the structure needs to have extra materials to make it more rigid, so any movement is imperceptible to human senses. (The current trick for supertalls is not to make the building perfectly rigid, but rather to use massive pendulums to slow down the swaying to a rate that can’t be detected.)
The Elevator Problem
Then there’s the elevator problem. Going taller means that, as some point, an additional elevator shaft needs to be created and filled with more elevators to move people to the higher floors. The developer must consider whether the lost rentable space and extra costs are less than the extra revenue from going taller. But, in general, taller building require more elevator equipment.
The Evidence
What does the evidence say about the structure of these costs? To look this, I have collected data for recently constructed buildings in New York, Chicago, and Shanghai (details here). The data set contains, for each building, the total cost of the structure and the number of floors; and from this we can look at how the average cost per floor changes as buildings go taller. In this way, we can infer something about the economics of skyscraper height. One caveat though; the sample sizes for each of these cities are very small, and they contain various types of structures, from public housing in Shanghai to supertall offices and luxury apartments. For this analysis, I only present the per floor costs without controlling for these other things. Please consider the findings as preliminary.
Costs in Three Cities
The first fact that pops out of this analysis is that it is much cheaper to build in Shanghai and Chicago than in New York City. The average price per floor for Chicago is about $6.2 million; for Shanghai it’s about $3.7 million per floor. For New York, on average, it costs about $15 million per floor. Or in other words, for a cost of $20 million per floor (on average), you can get a 65-story skyscraper in New York, while in Shanghai you can one that’s 120 stories. In Chicago, at that price, you can get a 100-story structure.
Second, the minimum point for each of these cities is different. The lowest per floor costs in New York about 32 floors. For Chicago, it’s at 55 floors. Shanghai doesn’t seem to have a turning point based on the data—with per floor costs rising at all levels. (Why this is requires further work.)
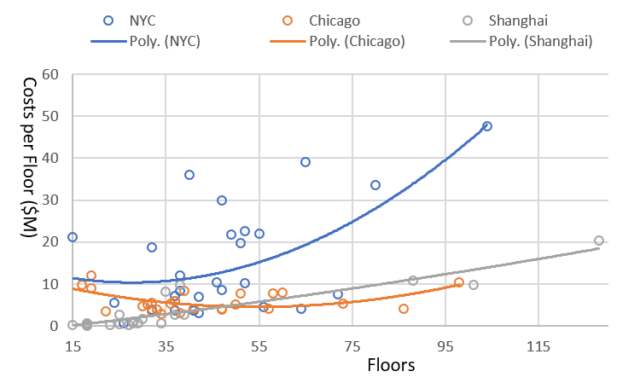
The Future of Height
It’s clear that the future of height is upward. Though we tend to focus on particular thresholds, like the first one-kilometer or one-mile high tower, these will eventually be achieved as long as two conditions hold. First is continued economic growth, which will bid up the value of central locations in cities around the world. And second is the on-going process of technological innovation which will lower the cost of providing height.
The fact that countries like the U.A.E, Saudi Arabia, and China could enter the skyscraper race in such short order is because they are able to tap into the global skyscraper complex of architects, engineers, banks, and other related institutions. These players rapidly spread information and know-how to newly developed countries that are aiming to grow their cities. The experiences with skyscraper building there then becomes part of the global knowledge base, further increasing the rate of technological change, and lowering the cost of construction. One of the reasons why New York City will never be able to compete anymore for the world’s tallest building (which it invented over a century ago) is because the rapid escalation in construction costs tend to erode any savings from technological improvements.
Ever Upwards
The rate and direction of technological change is difficult to measure, but I hope to measure and discuss it in a future post. Suffice it to say, however, that as long as the there’s the desire to go tall, humankind will find a way to get there. The economics of skyscraper height show this to be true.
Continue reading. The rest of the series can be read here.
—
[1] Normally, prices are quoted in dollars per square foot or meters. But for this analysis, I use per floor costs to illustrate the economics. So, for simplicity, assume that each floor in a skyscraper is fixed at 200’ x 100’=20,000 square feet (or about 1858 square meters), which is about the average floor size for a modern high rise in the U.S.
[…] have taken advantage of, and have driven, new technological innovations that allow buildings to be both taller and less expensive. We now turn to the evolution of some of this […]